Wireless Sensors Networks (WSN) offers many new possibilities for communication
with embedded devices and gadgets. WSN is often associated with Internet-Of-Things
(IoT) although researched for many years there are yet less applications for everyday
use. Designing, implementing and debugging WSN is very different and more complex
from more traditional networks. One should also keep in mind that WSN/IoT focus is
more on connectivity rather than bandwidth. The challenges include:
This document exploits some parts of WSN. It exemplifies the usage of small Microcontroller
(MCU) with a built-in radio transceiver for IEEE 802.15.4 (one of the standards for WSN). The
MCU is on custom PCB for a wide use of application. PCB is designed to be a flexible functional
unit with a built-in antenna, standard case and many options and each board can also become a
receiving (sink) node when attaching a TTL-to-USB cable. A custom easy-to-use firmware is discussed.
this is currently based on the Contiki operating system and Rime a very lightweight network
protocol used in Contiki. The PCB can be flashed with other code and operating systems.
Descriptions in this document refers to:
- PCB board revision 1.4
- Custom firmware revision 3.2
Sensor in standard case
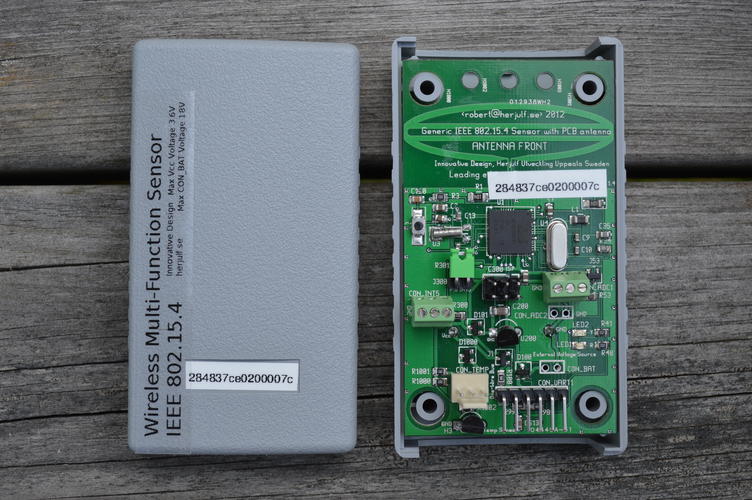
The sensor board suitable for data collection, monitoring and "Internet of things"
(IoT) type applications. MCU can be used with Contiki, TinyOs and other operating
systems. Board is preprogrammed with versatile and easy to use custom firmware,
based on Contiki Rime broadcast protocol. The radio coverage (following the IEEE
802.15.4 output power 3 mW) using the built-in PCB antenna is 300 meter line-of-sight.
(LOS) PCB is designed for a IP54 classed standard case but of course enclosures are
possible.
A very minimal wireless network
An absolute minimal usable wireless network needs:
- Two sensor/motes
- One FTDI 3.3V USB-TTL-cable. (TTL with 6 pin header)
Attaching TTL-USB-cable to one of sensors/mote turn this node into
a sink node. USB connects to a computer displaying and storing the
radio report. This node will also be powered from USB.
The other sensors/mote becomes simply the reporting mote.
Hardware description
- MCU AtMega128rfa1 with integrated IEEE 802.15.4 Transceiver.
- Integrated High-Performance PCB antenna. Supercardiod.
- Low-Power Voltage regulator for wide voltage input range.
- Direct power option. Max 3.6V bypassing the voltage reg.
- Hi-res 12 bit temp. sensor.
- Unique 64 bit ID via temp. sensor.
- 2 Analog inputs. ADC1/AD1, ADC2/AD2
- 1 Analog input to voltage regulator. CON_BAT/V_IN
- 1 GPIO/pulse pin. with jumper. selectable pull-up. P0.
- 1 Programmable power pin Vcc. via FET for external sensor.
- 1 GPIO with connector intended for one-wire bus.
- 2 LED's Red/Yellow for monitoring and debugging.
- Programmable via AVR 6-Pin (0.1"") ISP or via USB/serial bootloader.
- Compact size. PCB 80x45.5 mm. Case 90x50x32 mm standard case.
- Weight 20 gr without battery and holder including standard case 70 gr
- Optional on-board humidity sensor. Honeywell, Hih6130/Hih6131
- Optional on-board comparator typical use w. 0805 or 1206 phototrans. P1
PCB front view
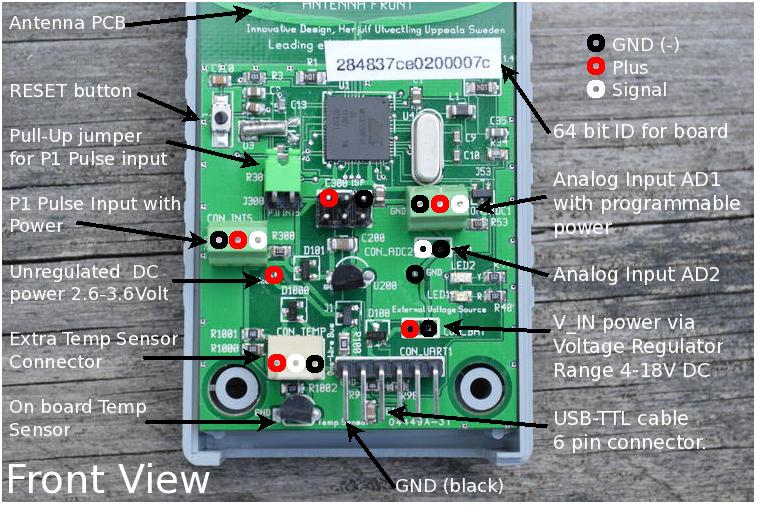
PCB rear view
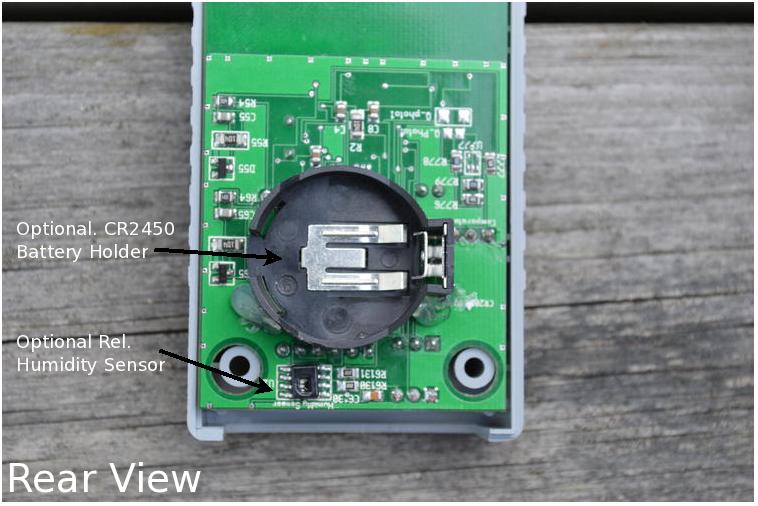
Quick start for the impatient
You'll need two or more nodes and a USB-TTL cable you're also set with the default settings.
- Connect one node to your computers terminal program via the USB-TTL cable
- Power the other node(s) with battery or use any other option.
Terminal programs include, minicom, hyperterminal. Baud 38400 bps, 1 stopbit
no parity, no flow-control. The node connected to USB will also be powered
from USB and will automatically report data from it's neighboring nodes.
Power options
External power options
Powering from external sources
- USB power. Using the USB-TTL cable with 6 pin header at bottom.
- Parasite power via voltage regulator. Marked CON_BAT. 3.5-18 Volt.
NOTE. CON_BAT voltage is measured as V_IN in firmware.
Battery power options
Via the regulated input through voltage regulator via CON_BAT.
- 6/12V lead acid or similar to CON_BAT.
- Lithium-ion 4.2V to CON_BAT.
Via the unregulated input through Vcc and GND pins on the PCB
- Coin Cell battery Lithium 3V CR2450 or similar via battery holder on back of PCB
- 2 Pcs in serial 3V AA or AAA alkaline batteries.
- 1 Pcs Lithium-thionyl chloride battery 3.6V (AA, AAA and other footprints)
- 1 Pcs LiFePO4 battery 3.3V (AA, AAA and other footprints)
- 2 Pcs in serial NiMH 2.8V
- CAUTION! Be aware that voltage above 3.6V will permanently damage your mote.
Sink node or receiving node
A receiving node (sink) is node that reports it's incoming data packets (reports)
from neighboring nodes. The reports are sent over USB. With the custom firmware a
sensor/mote automatically becomes a sink node when the USB-TTL cable is attached.
PCB USB-cable TTL-USB 6-pin connector.
To create a USB capable a device a FTDI USB-TTL cable is needed. The cable has
a standard type-A USB connector for host side. The sensor/mote side uses a
6 pin connector. See picture for how to connect. When cable is connected
to USB sensor get powered via USB. NOTE the custom firmware detects USB power
and turns mote into a sink mote by turning radio on and reporting
received data via USB.
NOTE. Disconnect the 6-pin header from sensor/mote when cable is not connected
to any host as the cable forces the MCU use much more power.
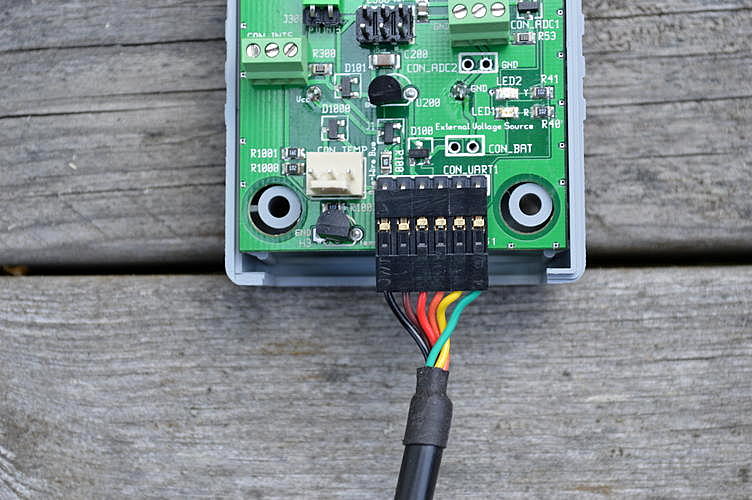
Battery lifetime
Battery lifetime is a crucial and challanging area. It's dependent on number of different factors among them:
- How the radio is used. Number of transmits, see report interval.
- Radio Duty Cycling (RDC).
- How MCU uses sleep modes.
- Sensors current consumption.
- Battery type.
- Temperature.
- Self discharge
- Battery discharge function.
Some approximative current consumption numbers seen with the sensor/mote using the custom firmware.
- 10 uA MCU PWR_SAVE Radio OFF
- 3 mA MCU IDLE Radio OFF
- 18 mA MCU Radio TX
The CR2450 coin cell battery that can mounted on the rear side it has a capacity
of about 450 mAh. Nominal voltage is 3V which is needed for the built-in
temp sensors. But seems to work to about 2.6V in most cases.
Expect a CR2450 with report interval of 1 min to keep up some week used with Pwr_save
sleep mode. Of course increasing the report interval increases the battery lifetime.
One can think of battery having a budget for a number of radio reports. It's recommended
to monitor the MCU battery voltage via the radio with the V_MCU report.
NOTE. The board has one power source under software control via FET.
This to enable power only when needed for a measurement.
Tips for debugging radio connectivity
Here you have to experiment a bit which a part of the WSN-life. Radio coverage at
line-of-sight (LOS) is about 300 m this with the PCB antennas oriented. But walls
and other hinders you have to test. For your help the custom firmware has
functions to help examine you the radio coverage.
- Using radio reports coming on the USB interface.
- Using LED's on the PCB.
When the sink node is connected to a terminal program (minicom, hyperterminal)
or by looking at the stored receiving packets in case sensd is installed.
Radio report include RSSI (Receiver Signal Strength Indicator) the higher
the better. The reports also the report contains LQI (Link Quality Indicator)
which indicates radio interference. The higher the better. See AtMega128rfa1
documentation for details.
You can use the debug function in firmware to flash LED's when packets are
received or transmitted. It's possible to walk around and check radio
coverage checking the RX LED. Set the report interval (ri in firmware) to about
10s and enable debug (de in firmware with the mask for D_RX) to blink every
RX-packet and move around and verify blinking and radio coverage.
It is also be useful to monitor RSSI/LQI via plots etc to understand the radio
environment in detail for seasonal and other changes.
Data collection and monitoring
Net topology
Broadcast network
Custom firmware implements a broadcast network currently using Contiki
Rime with radio reports in plain ASCII text. The data is formatted with
tag-style encoding. Both address and report should fit in one IEEE 802.15.4
packet of 127 bytes. So any mote following this scheme can be a part of the
network. Although one must make sure there are no address collisions. The
the PCB has a unique 64-bit ID via the temperature sensor and automatically
creates a unique Rime address based on this. As a single-hop-radio coverage
a broadcast network is simple and attractive and useful for many applications.
The advantages:
- Very simple setup.
- Very low power consumption.
- Robust.
The disadvantages:
- One-hop coverage.
- Sink nodes has radio on. High power consumption.
Each node is independent, MCU can be in very deep sleep mode and be woken
up by interrupt timer and read the sensors form a data report and broadcast.
The schema requires one or several sink nodes with full listening. They
consume much more power. The sink receives the received data and form
a URI and optionally store data in a file for later plotting and processing.
There is no retransmission of broadcast packets. It's suggested to monitor
packet sequential numbers for losses as well as RSSI and LQI for received
packets.
sensd code and unix version
Sensd is a daemon to collect and visualize data from the WSN. send uses the
USB connection to the sink node.
Via a combination of:
- URI (needs a web-server)
- datafile for plotting storage etc
The sensd package also contains some other useful utilities.
The code is stored in github:
It's recommended you read the documentation and README file. There are also
binary packages for Linux. Statically linked for x86 arch..
URI examples
sensd can display the received data in hierarchical file tree intended to
form an URI (Uniform resource identifier) for Internet access the file
tree needs a web-sever to form the full URI. The URI format an easy-to-use
and consistent way of accessing sensor data and align close to emerging IoT.
WSN node examples: (in use)
- From a solar driven node in the authors apple tree w. temp, humidity etc.
-
-
- http://www.herjulf.se/projects/sensor/WSN1-GW1/apple-tree/T
-
- Full apple-tree node URI's can be seen via:
-
- http://www.herjulf.se/projects/sensor/WSN1-GW1/apple-tree/
- Another node is monitoring UPS battery voltage:
-
- http://www.herjulf.se/projects/sensor/WSN1-GW1/UPS-battery-attic/V_IN
A plot and some more info are among Project Examples
- Another node is in a long term test for waster level/soil moisture:
-
- http://www.herjulf.se/projects/sensor/WSN1-GW1/soil-moisture/V_A1
The analog voltage is to be converted to the correct water level or soil moisture.
- Another node at house main power meter and reads the S0 interface:
-
- http://www.herjulf.se/projects/sensor/WSN1-GW1/main-AC-power/P0_T
Number of inpulses per secound. To be scaled to kW. See Project Examples.
NOTE. The combination sensd and a broadcast network does not give a
REST'ful service (client-server) rather we get a caching server.
Where we see data from the last received report.
Also note that the unique 64-bit ID is aliased with human readable
part in URI. This is done via a soft-link in the file system.
sensd on windows
There is a first port to Windows. More info will come.
sensd on RPi
Small, cheap and powerful SoC platforms. Raspberry Pi is one who
received a lot of attention. send builds nicely and runs but
there have been some stops which are currently under investigation.
Anyhow it's seems important to have sufficient and reliable power
for both powering the device as to have externally powered USB-hub.
Seems like the USB-TTL cable was able to reboot the RPi.
Below is a picture of authors effort. USB-hub glued on enlosure
and short wires.
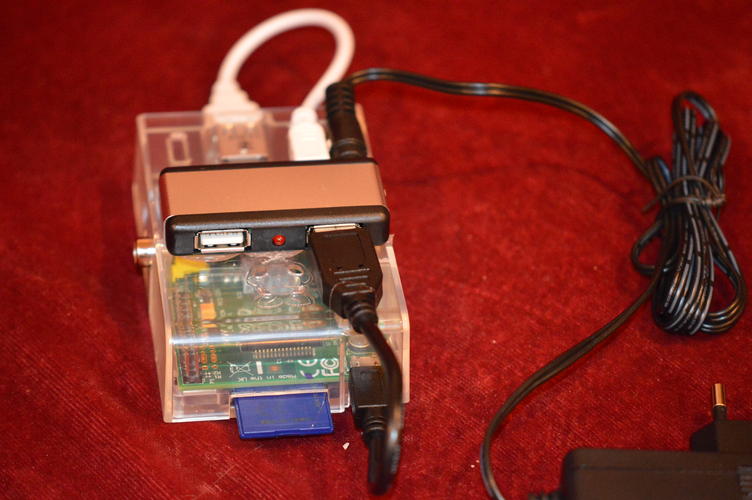
Custom firmware
The custom firmware controls the setting of the node, all settings
are stored the non-volatile memory EEPROM of the MCU. Operational-,
status-information, statistics and errors can be viewed via the firmware.
On sink nodes all radio report from neighbors are seen via the firmware
this is also where the sensd daemon gather it's information.
Much design and programming has been focused to debug and troubleshoot the WSN
network and the sensors.
Custom firmware: commands
There are many commands. Luckily you wont need most them but there are
couple of commands that most users probably would like to use. First
when using the firmware commands you have to connect to minicom, hyperterminal
or similar terminal program via the USB-TTL cable. (38400 1 stop bit and no parity
and no flow-control)
Basic commands
- Report interval. ri (how often)
- Report mask. re (what)
- System summary. ss
Report interval is the time in seconds. That the wakes up gathers data sends
a broadcast message. Report mask is bitmask in HEX thats controls what's data
is sent.
To verify the report mask when configuring the mote one can set report interval
temporary short to see that reports looks like expected.
The system summary command has general information about the mote.
- h - help
-
- v - version
-
- u - uptime
-
- aes [on|off] - integrety
- For test only.
- cali [[a1|a2|v_in] voltage] - calibrate
- Calibrate the analog readings from v_in, ADC1, ADC2. Volt.
- No argument just prints the current reads. v_in, ADC1, ADC2
- de [mask] - debug
- Enable debug. See separate section.
- hum - humidity sensor
- Read (optional) humidity sensor..
- hump [on|off] - humidity perm sensor pwr
- On. For normal operation.
- id [reset] - id handling
- Print unique 64 bit ID.
- mcu - mcu info
- MCU related debugging info for non-mortals
- ne [flush] - neighbor table
- List of neighboring nodes. Addr, last SEQ, RSSI and LQI.
- Can be useful in monitoring the network.
- Cache can be flushed. New entries are created automatically.
- Entries older than 200 seconds are removed.
- log [auto|on|off] - motes data on USB
- Override the automatic log. setting.
- Which starts printing on USB when you connect the USB-TTL cable.
- ow - one-wire sensors
- The temperature sensors. Onboard and optional..
- re [mask] - mote report setting
- Report mask. See separate section.
- ri [int] - report interval
- Report interval in seconds. How often the node broadcast it's data.
- rs - radio stats
- Radio stats from Contiki. Contiki docs for details
- ss - system summary
- System summary. A collection of major setting
- pwr1 [on|off] - pin1 pwr
- To manually interfere with the programmable power on ADC1
- Programmable power is used to enable a sensor just before reading. To save power.
- If used. It's recommended you use this together with corresponding debugging LED D_PWR1.
- rest - restore eeprom
- Revert settings to factory default. Typically after firmware upgrade.
- boot - reboot
- Restart the node
- upgr - reboot via bootloader
- Restart the node but wait in boot loader
Custom firmware: report mask
Report is a bitmask. It set by the re command in firmware
it crucial and control what data is used and sends from
the node. re command without any argument prints the current
setting. Stored in non-volatile EEPROM.
NOTE! due to limited size (127 bytes) of IEEE 802.15.4 packets
is recommended to keep report short. For trouble shooting
see de D_OPER and err command.
- R_ID - The unique 64 bit ID HEX
- R_T_MCU - MCU internal temperature in Celsius
- R_V_MCU - MCU voltage. Volt.
- R_P0 - Total numbers of interrupts on P0 input. HEX. 32 bit.
- R_P0_T - P0 number Interrupts per second last during last report interval. Decimal.
- R_P1 - Total numbers of interrupts on P1 input. HEX. 32 bit.
- R_P1_T - P1 number Interrupts per second last during last report interval. Decimal.
- R_UPTIME - Number of seconds since node started. HEX.
- R_RH - Relative humidity in percent. Decimal.
- R_V_IN - Input voltage on regulated power input. Decimal
- R_A1 - Input voltage on ADC1 input. Volt. Decimal
- R_A2 - Input voltage on ADC2 input. Volt. Decimal
Custom firmware: debug commands
Debug is a bitmask. It is set by the de command in firmware.
Several debug functions can be active concurrently. de command
expects a HEX value. de command without any bitmask prints the
current setting.
NOTE. That the debug setting is stored in EEPROM so rebooting
restores the previous setting.
Debug functions:
- Indication via a LED
- Printout via USB.
- D_OPER
- Prints out if report exceeds packet payload.
- D_RX
- When packed is received. Flashes the red LED and forces at print out.
- D_TX
- When a packet is sent. Flashes the yellow LED and forces at print out.
- D_PKT
- Not used
- D_OW
- Not used
- D_LED
- LED test turn Red and Yellow LED On.
- D_POWER
- Not used
- D_EVENT
- When a neighbor is removed due to garbage collection.
- D_P0_LED
- Flashes the red LED for pulse on input P0
- D_P1_LED
- Flashes the yellow LED for pulse on input P1
- D_AES
- Prints the AES key when sending a packet.
- D_PWR_1
- Programmable power. Turns the red LED on when PWR1 on.
Custom firmware: firmware upgrade, flashing
firmware upgrade, flashing
It's possible to use the built-in bootloader to use the node with other firmware and
operating systems. With the built-in bootloader one can simply use flash new code
via the USB-TTL cable. A typical use would be:
avrdude -p m128rfa1 -c avr109 -P /dev/ttyUSB0 -b 38400 -e -U flash:w:FIRMWARE.hex
See the section with HOWTO's for a more detailed information.
Programming: Pin assignments
- http://herjulf.se/products/WSN/sensors/documentation/HOWTO.pin_assignment_v1.4.h
See the section with HOWTO's for a more detailed information.
Contiki Platform Support
Atmega128rfa1 is a supported CPU in Contiki used in several board/platforms. There are
patches to support this board. Current work i maintained by Petter Skiden and hosted
in github. Platform is named avr-pluto. Platform has sample application for Rime
broadcast.
http://github.com/pskiden/contiki
Outdoor usage
External temp sensors
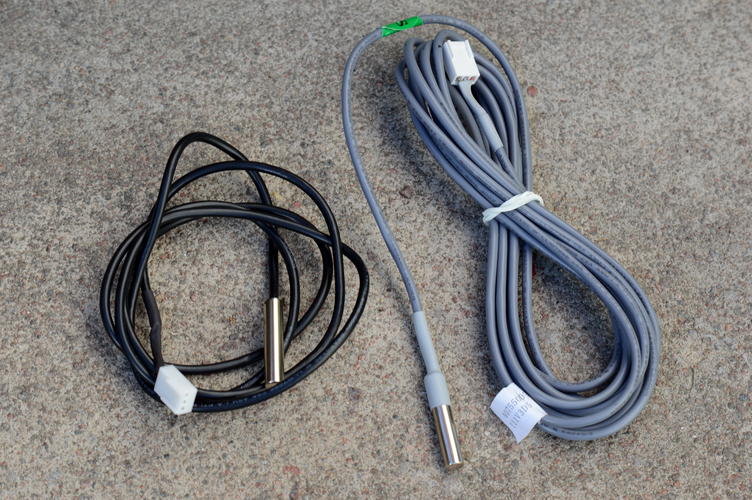
Picture shows two external temp. sensors The right sensor is waterproof and should
be able to use for water and soil temperature measurements. Sensors are connected to
PCB connector at posistion CON_TEMP. The temp. sensors uses external power via the
the builtin cable for maximum robustness.
Hardware hacking
Hardware hacking: Humidity sensor
The humidity sensor is expensive double the MCU price. For that reason the
sensor is optional. It's recommended that you get the board with the
humidity sensor if you intend to used it. Nevertheless it's possible for
people capable of SMD soldering but the device is fragile.
So you're on your own. Temperature 270C for some second. You should
also clean the PCB from old tin using a desoldering wick. The design
is currently using the Honeywell Hih6130/6131 sensors. The Hih6131 has
membrane and is considered as non-condensing.
The picture shows a Hih6131 mounted on the PCB.
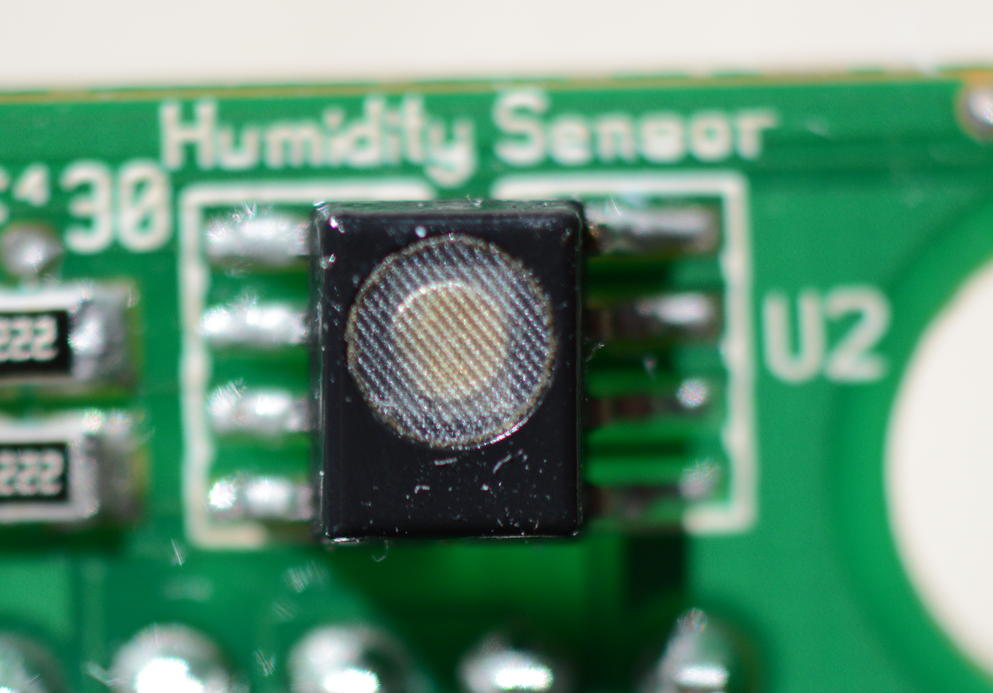
Solar driven I. using NiMH
Some installations have successfully used two NiMH batteries in series connected
to the unregulated input Vcc-GND. The charging voltage for a NiMH is about 1.42V
with two in series 2.84V. The MCU voltage when power via CON_BAT or via USB
is slightly above 3V. This violates the MiNh a bit but it seems to be working
well. We have this deployed in SGN (Serengeti Broadband Network) in Tanzania. [SBN]
- Two NiMH cells in series at the unregulated input
- Solar panel to CON_BAT the regulated input. Voltage 3.5 - 5V.
Hardware hacking: Solar driven II using LiFePO4
In some installations 3.3V or higher voltage is needed. This
is the case for the soil moisture sensors we're using.
It's with some hardware modification possible to increase the the
MCU voltage to 3.6V (the maximum MCU voltage). The charging voltage
for LiFePO4 is just 3.6V.
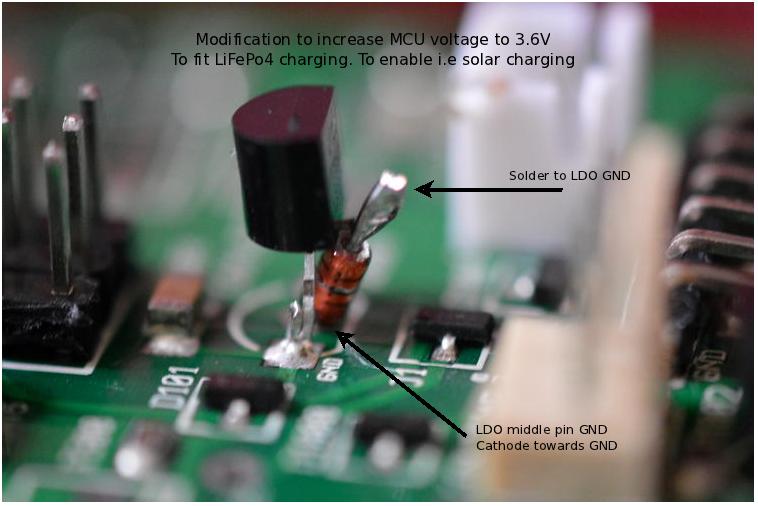
A battery pack created to fit the standard case:
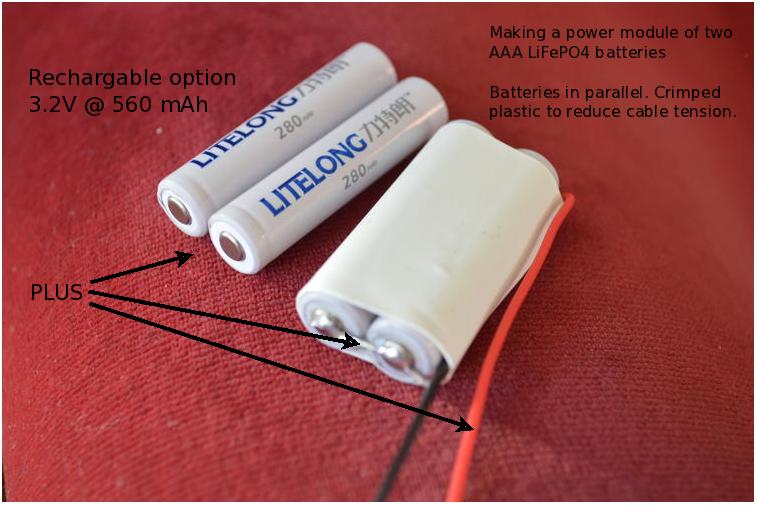
- One LiFePO4 at the unregulated input
- Solar panel to CON_BAT the regulated input. Voltage 3.5 - 5V.
You have size your solar panel accordingly. The climate in our country
more ore less forces this type of installation to be driven by daylight.
And even daylight is a precious resource. Currently a solar panel at
5V @ 500mA with LiFePO4 seems hold but darker times are to come.
Experiments are planned for Spain and Tanzania.
Hardware hacking: Comparator and phototransistor
This for hardened hardware geeks only. The pulse input P1 is
connected to an optional comparator on the rear side of the PCB.
Silk name is U777. The footprint is very hard to handle. But it's
possible to mount for SMD skilled personal. Be sure to clean
the footprint with desolder wick before soldering.
Close to the comparator there are to footprints
for phototransistors 1206 or 0806 footprints.
The author soldered two thin wires to a small PCB with the
photo transistor. The main reason to read the energy meter.
Luckily the provider Vattenfall has offered an S0 interface.
See the HOWTO section for more info.
Project and Examples
Project and Examples: Water level/soil moisture
Soil moisture and water level sensors that give an analog output can
be connected to any of the analog inputs CON_ADC1 or CON_ADC1.
The CON_ADC1 has an extra pin for programmable power.
The sensors power is controlled by the MCU. The idea here is to power up the
sensor only when it's needed. This to minimize the power used and maximize
battery lifetime. Programmable power is available on CON_ADC1. It enables
the power pin on CON_ADC1 one second before reading the analog signal
this to stabilize the electronics before reading he actual data.
There is an debug option to verify when power is enabled. See D_PWR_1
which turns the red LED on when the power is on.
-
Below is the wiring for Vegetronix VH400 soil moisture sensor.
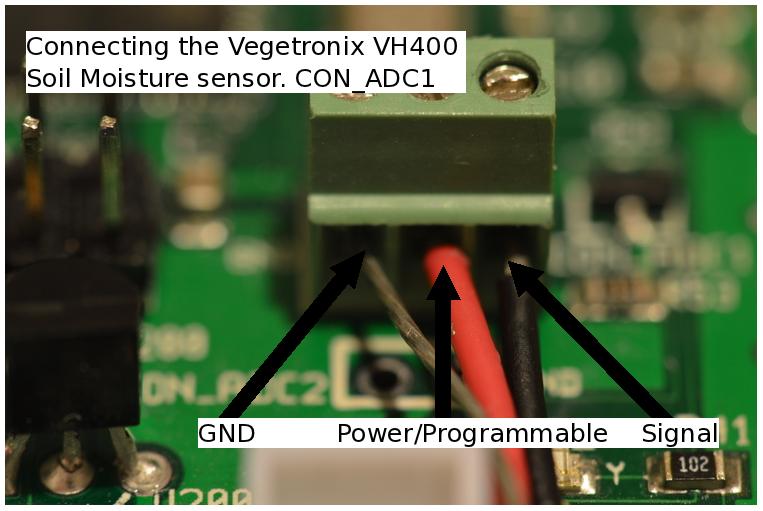
<
-
Below VH400 soil moisture sensor.
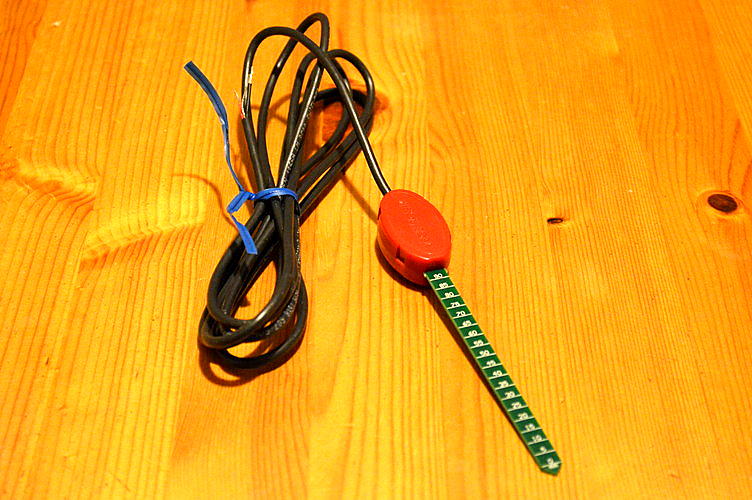
<
Project and Examples: Electricity use via power meter LED
See the section regarding comparator and phototransistor.
The photodiode was soldered to a veroboard in a sandwich contruction
to eliminate background light and cables connected to 1206 footprint
on the PCB. Attached to the power meter with adhesive tack.
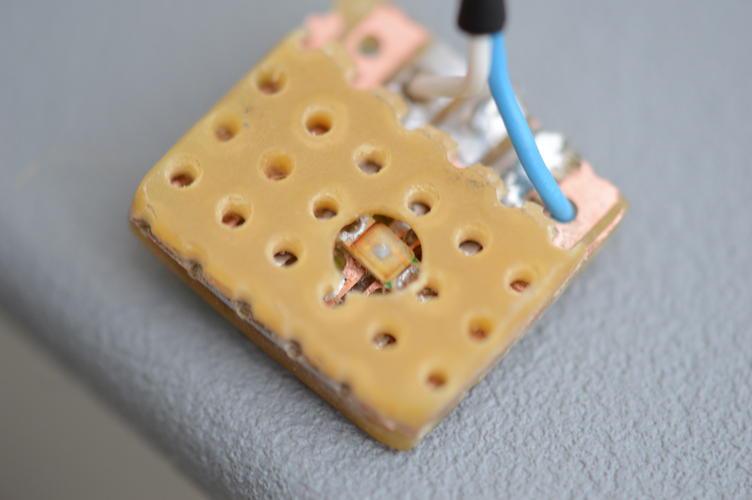
Under test. Below is a 13mm custom PCB with a photransistor.
Connecting to the photransistor.PCB
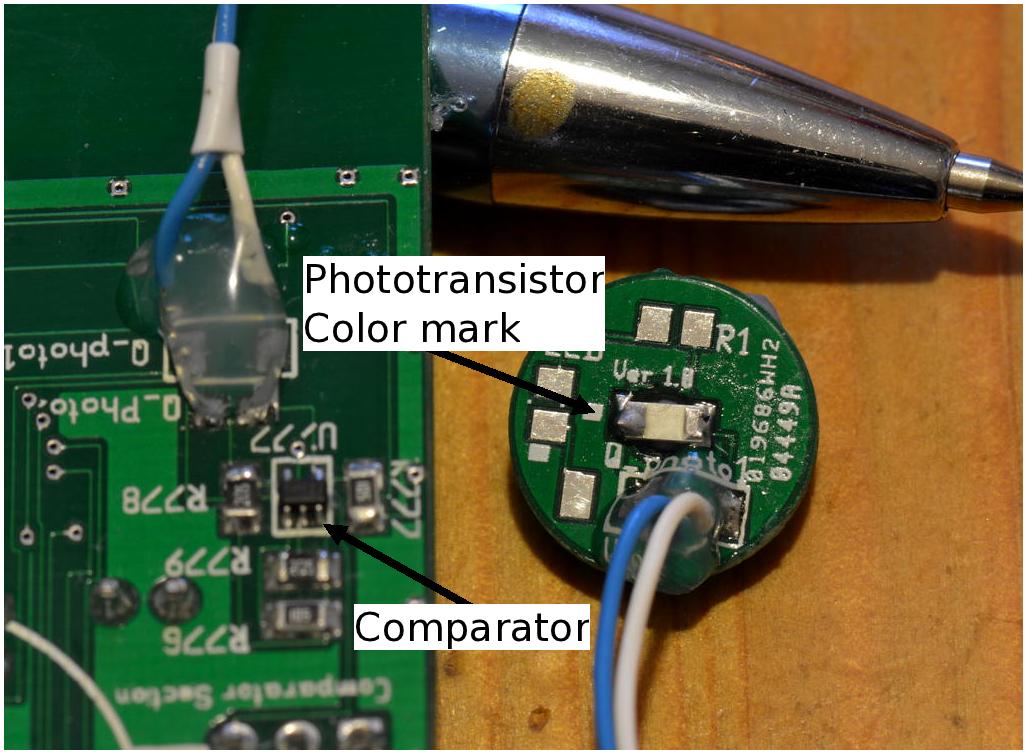
NOTE. The phototransistor back side was covered with black glue to avoid ambient light.
Also the phototransistor PCB needs a comparator on the node PCB. See picture.
Below is the result commented gnuplot of data collected via the
phototransistor and comparator to the P1 pulse input.
This power meter gives 1000 pulses/kWh plot is calibrated to kW.
One should note that reading a LED is a tricky process avoiding
background light etc. Better to use the S0-interface on P0 input
if possible.
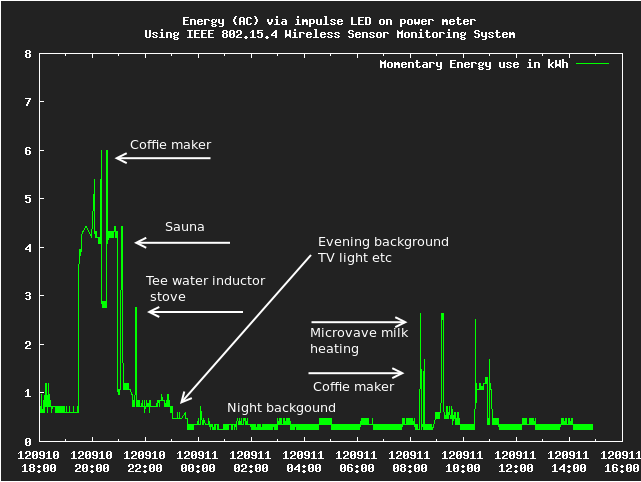
Project and Examples: Electricity use via S0 on power meter
To be written
http://www.herjulf.se/projects/sensor/WSN1-GW1/main-AC-power/P0_T
Number of inpulses per secound should be scaled to kW.
Project and Examples: UPS and battery monitoring
The mote is designed to measure the voltage to regulated power. Using
this parasite power option it's very easy to monitor battery and UPS.
Below a lead-acid battery for low-power server is monitored.
A gnuplot with battery voltage and temp:
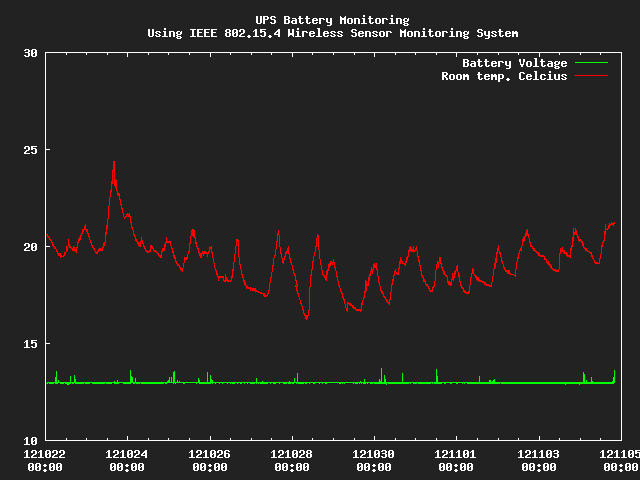
Project and Examples: Barometer I2C Module
There are relive cheap and accurate pressure modules to make an versatile
barometer or altitude meter. Check out the Bosh BMP085 specs. It has I2C
communications. There are modules to buy. Here we need some soldering skills
to replace the humidity sensor at rear of the PCB.
Also the battery holder is removed to make a robust mounting for the module.
Custom firmware support for BMP085.
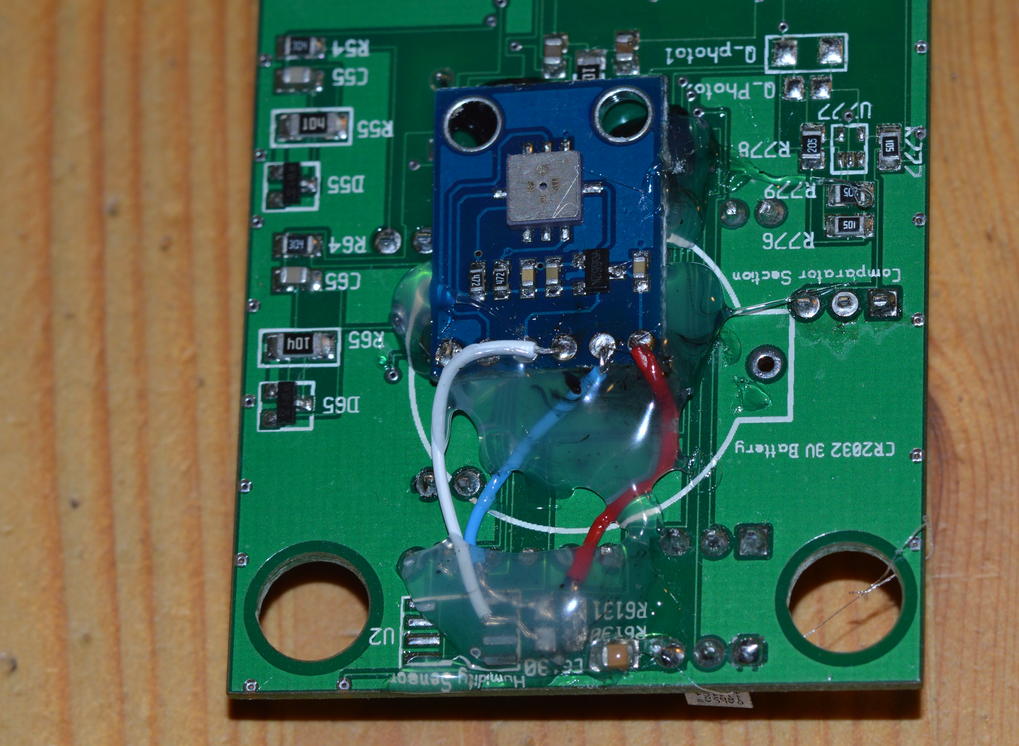
Project and Examples: Light measurement and pyranometers
One can add photodiodes to the analog inputs. ADC1, ADC2 either soldering
directly to the connector via a cable. Photodiodes comes in many footprints
though-hole or SMD.
Application also effects design. If monitoring ambient light a SMD diode most
most likely be enough. For more pyranometer applications rugged photodiodes with
larger exposed is better.
Regardless of size most likely a shunt resistor will be needed to read
photometric power and not open voltage. Shunt resistor must match the size
of the photodiode. Some experimentation might need. See also the HOWTO section.
Example with and an external photodiode for solar power monitoring:
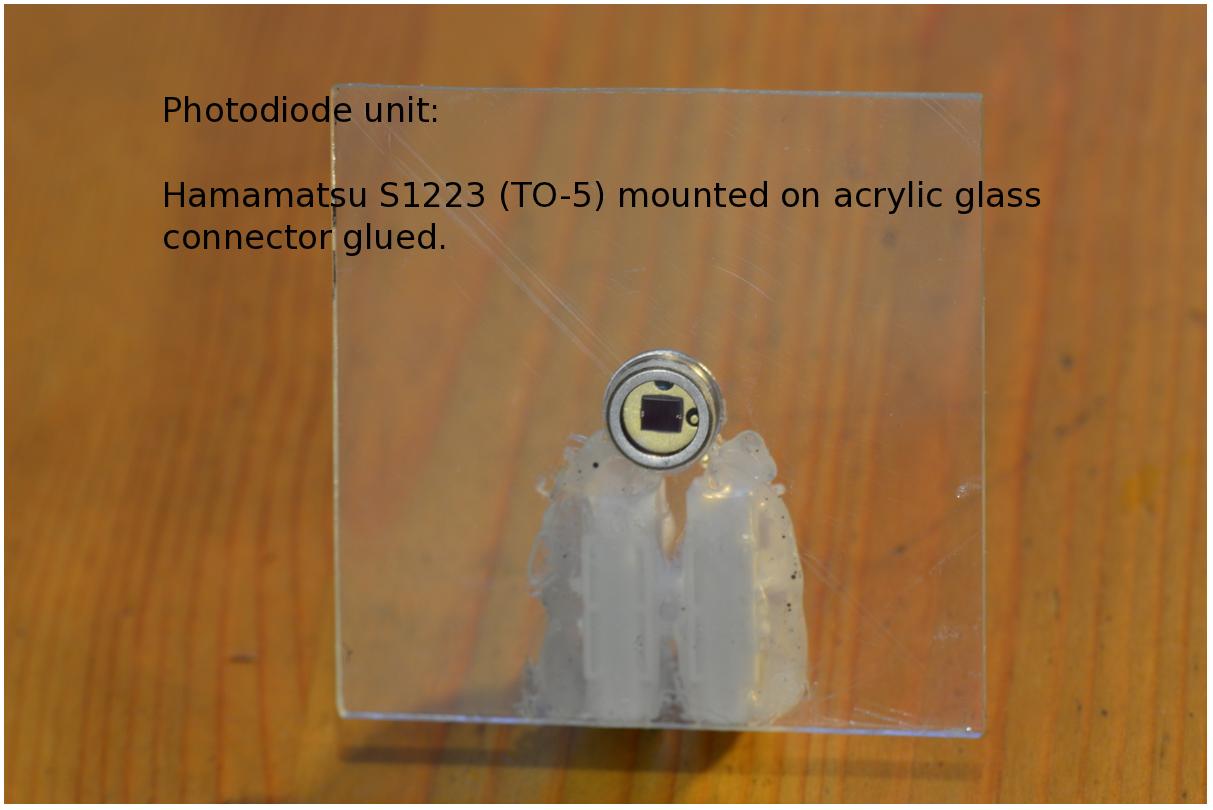
Example with and an SMD for ambient monitoring:
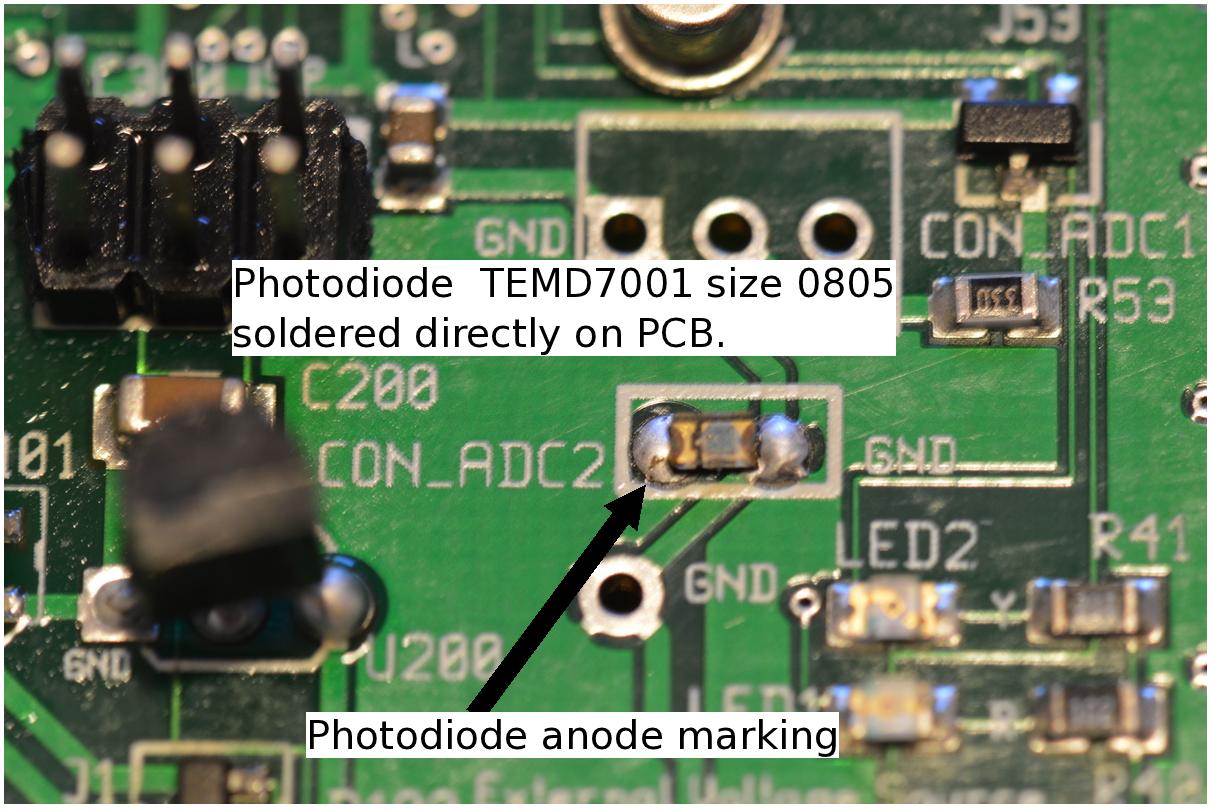
Some of the decanned transistors used:
The author has done some tests, yet without any usable results.
Project and Examples: Wind monitoring
Project and Examples: Radiation measurements
It should be possible to use the pulse input to report, nuclear radiation
for wireless typically alpha is interesting for radon monitoring. There have
been interesting work how transistors like 2N3055 can be used as sensors
Some of the decanned transistors used:
The author has done some tests, yet without any usable results.
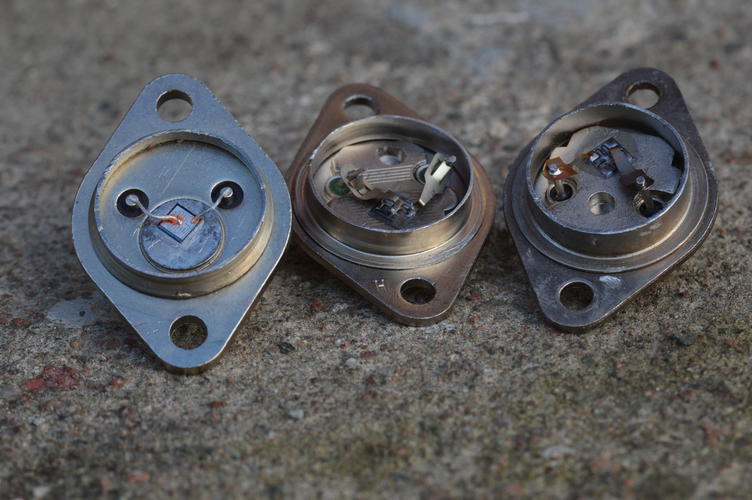
Here is another alternative from teviso.com in Switzerland. Straight forward to connect the sensor node. Just three wires are needed. The low voltage version RD3024 should best to use.
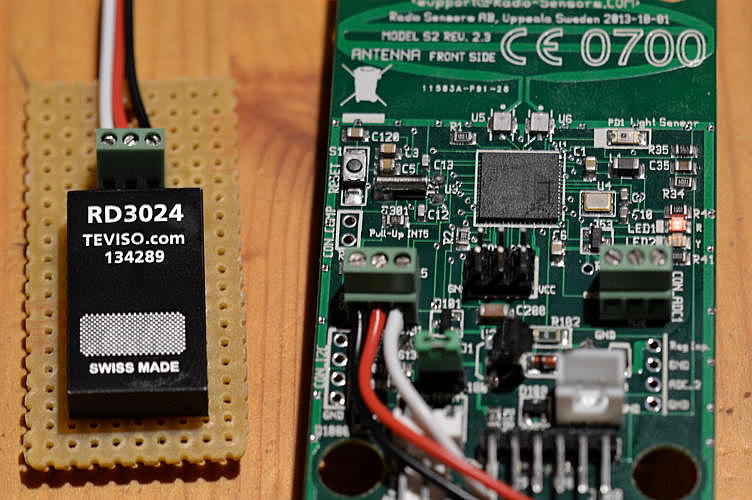
Product info via:
www.teviso.com
Scientific Gateway Effort
Project for common interface with authentication, meta-data, retrieval and presentation.
The idea is to provide a common interface for multidisciplinary areas. Data collections
and monitoring is one part of the work.
Product info via:
Sensordata collected via SSVL at KTH in Stockholm
Future work
IETF is currently standardizing Constrained Application Protocol CoAP. This seems to be an
important step for IoT. It would be nice to follow that path to have a very close or
even use some parts of the standard for example payload encoding. But CoAP has today
only mapping IP ipv4 and ipv6 but not the lightweight Rime protocol also used in Contiki.
Nevertheless Contiki/Rime together with sensd is capable to form URI's and functionally
work as a CoAP caching (due to asynchronous broadcast) server.
Real usage and reference installations
See also the the Scientific gateway:
Known bugs and caveats
- P0, P1 only works. Sleep mode IDLE. See firmware command to force IDLE. (FIXED in Model S2)
References
- Adam Dunkels. Rime - a lightweight layered communication stack for sensor networks. In Proceedings of the European Conference on Wireless Sensor Networks (EWSN), Poster/Demo session, Delft, The Netherlands, January 2007.
- ATmega128RFA1- Atmel Corporationâ. [Online]. Available: http://www.atmel.com/devices/ATMEGA128RFA1.aspx. [Accessed: 21-February-2012].
- Atmel AVR2006: Design and characterization of the. Radio Controller Board's 2.4GHz PCB Antenna.
- [Add authors] Inclusive Ubiquitous Access - A Status Report, Africom, Younde, Nov 2012
- [SBN] IL2213 WSN-Projects Fall 2011. [Online]. Available: http://www.tslab.ssvl.kth.se/csd/files/wsn/index.html. [Accessed: 21-February-2012].
- The Contiki O. [Online]. Available: http://www.contiki-os.org/. [Accessed: 29-February-2012].
- IEEE 802.15.4. [Online]. Available: http://www.ieee802.org/15/pub/TG4.html. [Accessed: 21-February-2012].
- R. Olsson and J. Laas, Sensd. 20120610, Available at https://github.com/herjulf/sensd.
- draft-ietf-core-coap-12. [Online]. Available: https://datatracker.ietf.org/doc/draft-ietf-core-coap/. [Accessed: 15-October-2012].
- M. Kovatsch, S. Duquennoy, and A. Dunkels, A Low-Power CoAP for Contikiâ in Mobile Adhoc and Sensor Systems (MASS), 2011 IEEE 8th International Conference on, 2011, pp. 855-860, DOI:10.1109/MASS.2011.100.
- Future Technology Devices International Limited (FTDI), TTL to USB Serial Converter Range of Cables Datasheet. 20100902, Available at http://www.ftdichip.com/Support/Documents/DataSheets/Cables/DS_TTL-232R_CABLES.pdf.
- User Datagram Protocol. [Online]. Available: http://www.ietf.org/rfc/rfc768.txt. [Accessed: 26-May-2012].
- IANA: RFCUniform Resource Identifier (URI) Schemes. [RFC4395]
- 6lowPAN The Wireless Embedded Internet, Z. Shelby, C. Borman Nov. 2009
- 6lowPAN http://datatracker.ietf.org/wg/6lowpan/charter
HOWTO's and other resources
A list of tips and HOWTO's